扭轉彈簧介紹
轉彈簧屬於螺旋彈簧,扭轉彈簧可以存儲和釋放角能量或者通過繞簧體中軸旋轉力臂以靜態固定某一裝置。這類彈簧通常是密身的,但是,簧圈之間有節距以減少摩擦。它們對旋轉或旋轉外力產生阻力。根據套用要求,設計扭轉彈簧的旋向(順時針或逆時針),從而確定彈簧的旋向。
主要參數
d (彈簧線徑) :該參數描述了彈簧線的直徑。
Dd (心軸最大直徑):該參數描述的是工業套用中彈簧軸的最大直徑,公差±2%。
Di (內徑): 彈簧的內徑等於外徑減去兩倍的線徑。扭簧在工作過程中,內徑可以減小到心軸直徑,
內徑公差±2%。
De (外徑) : 等於內徑加上兩倍的線徑。扭簧在工作過程中,外徑將變小,公差(±2%±0.1)mm。
L0 (自然長度):注意:在工作過程中自然長度會減小,公差±2%。
Ls (支承長度): 這是從彈簧圈身中軸到彈簧支承的長度,公差±2%。
An (最大扭轉角度):扭轉彈簧的最大扭轉角度,公差±15度。
Fn (最大負荷):允許作用在扭轉彈簧支承上的最大力,公差±15%。
Mn (最大扭矩): 最大允許扭矩(牛頓*毫米),公差±15%。
R (彈簧剛度): 這個參數確定彈簧工作時的阻力。單位 牛頓 * 毫米/度,公差±15%。
A1 & F1 & M1 :(扭轉角度,負荷和扭矩) : 以下公式可算出扭轉角度A1 = M1/R. 知道負荷,可用公式M = F*Ls計算扭矩。
支承位置 :扭轉彈簧的支承有四個位置:0°, 90°,180°和 270°
螺旋方向 : 右旋彈簧反時針方向旋,左旋彈簧順時針方向旋。我們的所有彈簧兩種旋向都可生產。
彈簧件號 : 每種彈簧都有對應編號 : 類別 . (De * 10) . (d * 100) . (N * 100) . 對於右旋的彈簧,相關記號為D。對於左旋的彈簧,相關記號為 G。N 記號表示圈數。例如:D.028.020.0350 件號表示右旋扭簧,外徑2.8 mm, 不鏽鋼線徑0.9 mm,共有3.5圈。
性能因數
性能因數: 彈簧剛度,最大變形量,最大負荷和旋向規格。
彈簧剛度是指,單位角位移產生的角回程扭矩。
最大變形量是指彈簧受損前最大變形量。
扭轉彈簧旋向為右旋,左旋和雙旋。
套用
扭轉彈簧是一種利用彈性來工作的機械零件。一般用彈簧鋼製成。用以控制機件的運動、緩和衝擊或震動、貯蓄能量、測量力的大小等 廣泛套用於計算機,電子,家電,照相機,儀器,門,機車,收割機,汽車,等行業!
生產設備主要設備有:數位化控制多功能電腦卷簧機、機械自動卷簧機、磨簧機、熱處理設備、大型熱卷彈簧生產線、質量檢測儀器。
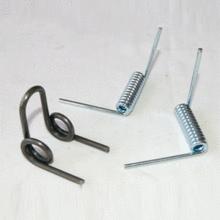
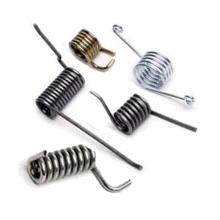
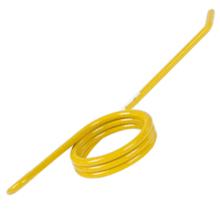

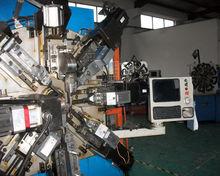
斷裂原因分析
斷裂原因
扭轉彈簧在電鍍鋅初期局部產生非正常組織馬氏體,由於馬氏體存在組織應力,與在酸洗和電鍍鋅時彈簧基體中的氫造成的內應力相互作用,導致扭轉彈簧出現裂紋並滯後斷裂。彈簧鋼絲生產的扭轉彈簧在客戶裝配前發現少量彈簧斷裂,如圖1 所示,斷口位置如箭頭所指。
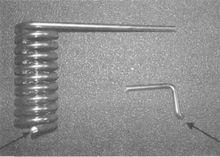
扭轉彈簧生產工藝: 彈簧鋼絲→繞簧→低溫去應力退火→高溫除油→水洗→稀鹽酸洗→水洗→電鍍鋅( 80 min) →水洗→下料→去氫處理( 200 ℃,4 h) →上料→水洗→彩色鈍化→水洗→烘乾→下料→檢查。
通過對金相組織及顯微硬度分析可知,彈簧斷裂處和附近裂紋處金相組織為馬氏體。由於馬氏體組織應力較大,易形成應力集中區域,而且馬氏體組織的氫脆敏感性比貝氏體和珠光體大,容易發生氫致沿晶斷裂[4 - 5]。馬氏體的形成應當是在電鍍鋅初期由於彈簧與電極之間產生電弧,造成彈簧局部產生電灼傷,在電灼傷部位的瞬時高溫超過奧氏體化溫度,隨後在電鍍溶液中急冷,使扭轉彈簧產生非正常的馬氏體組織。此外,扭轉彈簧在酸洗和電鍍鋅過程中,不可避免地存在析氫滲氫過程[6],析出的氫一部分以氫分子形式逸出表面,另一部分吸附於彈簧表面,並向彈簧基體內部擴散。進入基體的氫原子在位錯、晶界、夾雜物等處逐漸積聚,相互結合產生氫分子,隨著氫分子濃度的不斷增大,致使晶格扭曲,產生很大的內應力[7]。由於彈簧基體中存在較高濃度的氫和電鍍鋅過程中產生的馬氏體相互作用,造成扭轉彈簧出現裂紋並導致滯後斷裂。裂紋和斷裂造成鍍層和基體之間出現鍍鋅層脫落。
生產工藝改進建議:
( 1) 扭轉彈簧酸洗時,防止過腐蝕,酸洗液中添加的緩蝕劑既要有較強的緩蝕作用,又要有較強的抗氫滲透率。
( 2) 電鍍鋅過程中,嚴格操作規程,防止出現馬氏體; 在保證鍍層質量的前提下,儘量縮短電鍍鋅的時間。
( 3) 電鍍鋅後,儘量縮短鍍後和去氫處理的時間間隔,採用有效的除氫工藝。
( 4) 改進電極防護措施,避免產生電弧。