貼片介紹
SMT貼片指的是在PCB基礎上進行加工的系列工藝流程的簡稱。PCB(Printed Circuit Board)為印刷電路板。
SMT是表面組裝技術(表面貼裝技術)(Surface Mounted Technology的縮寫),是電子組裝行業里最流行的一種技術和工藝。電子電路表面組裝技術(Surface Mount Technology,SMT),稱為表面貼裝或表面安裝技術。它是一種將無引腳或短引線表面組裝元器件(簡稱SMC/SMD,中文稱片狀元器件)安裝在印製電路板(Printed Circuit Board,PCB)的表面或其它基板的表面上,通過再流焊或浸焊等方法加以焊接組裝的電路裝連技術。
在通常情況下我們用的電子產品都是由pcb加上各種電容,電阻等電子元器件按設計的電路圖設計而成的,所以形形色色的電器需要各種不同的smt貼片加工工藝來加工 。
SMT基本工藝
錫膏印刷--> 零件貼裝-->回流焊接-->AOI光學檢測--> 維修--> 分板。
電子產品追求小型化,以前使用的穿孔外掛程式元件已無法縮小。 電子產品功能更完整,所採用的積體電路(IC)已無穿孔元件,特別是大規模、高集成IC,不得不採用表面貼片元件。 產品批量化,生產自動化,廠方要以低成本高產量,出產優質產品以迎合顧客需求及加強市場競爭力 電子元件的發展,積體電路(IC)的開發,半導體材料的多元套用。 電子科技革命勢在必行,追逐國際潮流。可以想像,在intel、amd等國際cpu、圖象處理器件的生產商的生產工藝精進到20幾個納米的情況下,smt這種表面組裝技術和工藝的發展也是不得以而為之的情況。
smt貼片加工的優點:組裝密度高、電子產品體積小、重量輕,貼片元件的體積和重量只有傳統插裝元件的1/10左右,一般採用SMT之後,電子產品體積縮小40%~60%,重量減輕60%~80%。 可靠性高、抗振能力強。焊點缺陷率低。高頻特性好。減少了電磁和射頻干擾。易於實現自動化,提高生產效率。降低成本達30%~50%。節省材料、能源、設備、人力、時間等。
正是由於smt貼片加工的工藝流程的複雜,所以出現了很多的smt貼片加工的工廠,專業做smt貼片的加工,在深圳,得益於電子行業的蓬勃發展,smt貼片加工成就了一個行業的繁榮。
流程
SMT基本工藝構成要素包括:絲印(或點膠),貼裝(固化),回流焊接,清洗,檢測,返修
1、絲印:其作用是將焊膏或貼片膠漏印到PCB的焊盤上,為元器件的焊接做準備。所用設備為絲印機(絲網印刷機),位於SMT生產線的最前端。
2、點膠:它是將膠水滴到PCB板的固定位置上,其主要作用是將元器件固定到PCB板上。所用設備為點膠機,位於SMT生產線的最前端或檢測設備的後面。
3、貼裝:其作用是將表面組裝元器件準確安裝到PCB的固定位置上。所用設備為貼片機,位於SMT生產線中絲印機的後面。
4、固化:其作用是將貼片膠融化,從而使表面組裝元器件與PCB板牢固粘接在一起。所用設備為固化爐,位於SMT生產線中貼片機的後面。
5、回流焊接:其作用是將焊膏融化,使表面組裝元器件與PCB板牢固粘接在一起。所用設備為回流焊爐,位於SMT生產線中貼片機的後面。
6、清洗:其作用是將組裝好的PCB板上面的對人體有害的焊接殘留物如助焊劑等除去。所用設備為清洗機,位置可以不固定,可以線上,也可不線上。
7、檢測:其作用是對組裝好的PCB板進行焊接質量和裝配質量的檢測。所用設備有放大鏡、顯微鏡、線上測試儀(ICT)、飛針測試儀、自動光學檢測(AOI)、X-RAY檢測系統、功能測試儀等。位置根據檢測的需要,可以配置在生產線合適的地方。
8、返修:其作用是對檢測出現故障的PCB板進行返工。所用工具為烙鐵、返修工作站等。配置在生產線中任意位置。
貼片工藝
單面組裝
來料檢測 => 絲印焊膏(點貼片膠)=> 貼片 => 烘乾(固化)=> 回流焊接 =>清洗 => 檢測 => 返修
雙面組裝
A:來料檢測 => PCB的A面絲印焊膏(點貼片膠)=> 貼片 PCB的B面絲印焊膏(點貼片膠)=> 貼片 =>烘乾 => 回流焊接(最好僅對B面 => 清洗 => 檢測 => 返修)。
B:來料檢測 => PCB的A面絲印焊膏(點貼片膠)=> 貼片 => 烘乾(固化)=>A面回流焊接 => 清洗 => 翻板 = PCB的B麵點貼片膠 => 貼片 => 固化 =>B面波峰焊 => 清洗 => 檢測 => 返修)
此工藝適用於在PCB的A面回流焊,B面波峰焊。在PCB的B面組裝的SMD中,只有SOT或SOIC(28)引腳以下時,宜採用此工藝。
單面混裝工藝
來料檢測 => PCB的A面絲印焊膏(點貼片膠)=> 貼片 =>烘乾(固化)=>回流焊接 => 清洗 => 外掛程式 => 波峰焊 => 清洗 => 檢測 => 返修
雙面混裝工藝
A:來料檢測 =>PCB的B麵點貼片膠 => 貼片 => 固化 => 翻板 => PCB的A面外掛程式=> 波峰焊 => 清洗 => 檢測 => 返修
先貼後插,適用於SMD元件多於分離元件的情況
B:來料檢測 => PCB的A面外掛程式(引腳打彎)=> 翻板 => PCB的B麵點貼片膠 =>貼片 => 固化 => 翻板 => 波峰焊 => 清洗 => 檢測 => 返修
先插後貼,適用於分離元件多於SMD元件的情況
C:來料檢測 => PCB的A面絲印焊膏 => 貼片 => 烘乾 => 回流焊接 =>外掛程式,引腳打彎 => 翻板 => PCB的B麵點貼片膠 => 貼片 => 固化 => 翻板 => 波峰焊 =>清洗 => 檢測 => 返修A面混裝,B面貼裝。
D:來料檢測 =>PCB的B麵點貼片膠 => 貼片 => 固化 => 翻板 =>PCB的A面絲印焊膏 => 貼片 => A面回流焊接 => 外掛程式 => B面波峰焊 => 清洗 => 檢測 =>返修A面混裝,B面貼裝。先貼兩面SMD,回流焊接,後插裝,波峰焊 E:來料檢測 => PCB的B面絲印焊膏(點貼片膠)=> 貼片 => 烘乾(固化)=>回流焊接 => 翻板 => PCB的A面絲印焊膏 => 貼片 => 烘乾 =回流焊接1(可採用局部焊接)=> 外掛程式 => 波峰焊2(如插裝元件少,可使用手工焊接)=> 清洗 =>檢測 => 返修A面貼裝、B面混裝。
雙面組裝工藝
A:來料檢測,PCB的A面絲印焊膏(點貼片膠),貼片,烘乾(固化),A面回流焊接,清洗,翻板;PCB的B面絲印焊膏(點貼片膠),貼片,烘乾,回流焊接(最好僅對B面,清洗,檢測,返修)
此工藝適用於在PCB兩面均貼裝有PLCC等較大的SMD時采。
B:來料檢測,PCB的A面絲印焊膏(點貼片膠),貼片,烘乾(固化),A面回流焊接,清洗,翻板;PCB的B麵點貼片膠,貼片,固化,B面波峰焊,清洗,檢測,返修)此工藝適用於在PCB的A面回流。
薄膜印刷線路
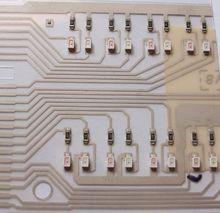
此類薄膜線路一般是用銀漿在PET上印刷線路。在此類薄膜線路上貼上黏貼電子元器件有兩種工藝工法,一種謂之傳統工藝工法即3膠法(紅膠、銀膠、包封膠)或2膠法(銀膠、包封膠),另一種謂之新工藝即1膠法---顧名思義,就是用一種膠即可完成貼上黏貼電子元器件,而不再用3種膠或2種膠。此新工藝關鍵是使用一種新型導電膠,完全具有錫膏的導電性能和工藝性能;使用時完全兼容現行的SMT刷錫膏作業法,毋需添加任何設備。
選取
概述
表面安裝元器件的選擇和設計是產品總體設計的關鍵一環,設計者在系統結構和詳細電路設計階段確定元器件的電氣性能和功能,在SMT設計階段應根據設備及工藝的具體情況和總體設計要求確定表面組裝元器件的封裝形式和結構。表面安裝的焊點既是機械連線點又是電氣連線點,合理的選擇對提高PCB設計密度、可生產性、可測試性和可靠性都產生決定性的影響。
表面安裝元器件在功能上和插裝元器件沒有差別,其不同之處在於元器件的封裝。表面安裝的封裝在焊接時要經受耐高溫度的元器件和基板必須具有匹配的熱膨脹係數。這些因素在產品設計中必須全盤考慮。
選擇合適的封裝,其優點主要是:
1)有效節省PCB面積;
2)提供更好的電學性能;
3)對元器件的內部起保護作用,免受潮濕等環境影響;
4)提供良好的通信聯繫;
5)幫助散熱並為傳送和測試提供方便 。
表面安裝元器件選取
表面安裝元器件分為有源和無源兩大類。按引腳形狀分為鷗翼型和“J”型。下面以此分類闡述元器件的選取。
無源器件
無源器件主要包括單片陶瓷電容器、鉭電容器和厚膜電阻器,外形為長方形或園柱形。園柱形無源器件稱為“MELF”,採用再流焊時易發生滾動,需採用特殊焊盤設計,一般應避免使用。長方形無源器件稱為“CHIP”片式元器件,它的體積小、重量輕、抗菌素衝擊性和抗震性好、寄生損耗小,被廣泛套用於各類電子產品中。為了獲得良好的可焊性,必須選擇鎳底阻擋層的電鍍。
有源器件
表面安裝晶片載體有兩大類:陶瓷和塑膠。
陶瓷晶片封裝的優點是:
1)氣密性好,對內部結構有良好的保護作用;
2)信號路徑較短,寄生參數、噪聲、延時特性明顯改善;
3)降低功耗。
缺點是因為無引腳吸收焊膏溶化時所產生的應力,封裝和基板之間CTE失配可導致焊接時焊點開裂。最常用的陶瓷餅片載體是無引線陶瓷習片載體LCCC。
塑膠封裝被廣泛套用于軍、民品生產上,具有良好的性價比。其封裝形式分為:小外形電晶體SOT;小外形積體電路SOIC;塑封有引線晶片載體PLCC;小外形J封裝;塑膠扁平封裝PQFP。
為了有效縮小PCB面積,在器件功能和性能相同的情況下首選引腳數20以下的SOIC,引腳數20-84之間的PLCC,引腳數大於84的PQFP。
減少故障
製造過程、搬運及印刷電路組裝 (PCA) 測試等都會讓封裝承受很多機械應力,從而引發故障。隨著格柵陣列封裝變得越來越大,針對這些步驟應該如何設定安全水平也變得愈加困難。
多年來,採用單調彎曲點測試方法是封裝的典型特徵,該測試在 IPC/JEDEC-9702 《板面水平互聯的單調彎曲特性》中有敘述。該測試方法闡述了印刷電路板水平互聯在彎曲載荷下的斷裂強度。但是該測試方法無法確定最大允許張力是多少。
對於製造過程和組裝過程,特別是對於無鉛 PCA 而言,其面臨的挑戰之一就是無法直接測量焊點上的應力。最為廣泛採用的用來描述互聯部件風險的度量標準是毗鄰該部件的印刷電路板張力,這在 IPC/JEDEC-9704 《印製線路板應變測試指南》中有敘述。
若干年前英特爾公司意識到了這一問題並開始著手開發一種不同的測試策略以再現實際中出現的最糟糕的彎曲情形。其他公司如惠普公司也意識到了其他測試方法的好處並開始考慮與英特爾公司類似的想法。隨著越來越多的晶片製造商和客戶認識到,在製造、搬運與測試過程中用於最小化機械引致故障的張力限值的確定具有重要價值,該方法引起了大家越來越多的興趣。
隨著無鉛設備的用途擴大,用戶的興趣也越來越大;因為有很多用戶面臨著質量問題。
隨著各方興趣的增加,IPC 覺得有必要幫助其他公司開發各種能夠確保BGA在製造和測試期間不受損傷的測試方法。這項工作由 IPC 6-10d SMT 附屬檔案可靠性測試方法工作小組和 JEDEC JC-14.1 封裝設備可靠性測試方法子委員會攜手開展,該工作已經完成。
該測試方法規定了以圓形陣列排布的八個接觸點。在印刷電路板中心位置裝有一 BGA 的 PCA 是這樣安放的:部件面朝下裝到支撐引腳上,且負載施加於 BGA 的背面。根據 IPC/JEDEC-9704 的建議計量器布局將應變計安放在與該部件相鄰的位置。
PCA 會被彎曲到有關的張力水平,且通過故障分析可以確定,撓曲到這些張力水平所引致的損傷程度。通過疊代方法可以確定沒有產生損傷的張力水平,這就是張力限值。
封裝材料
通常封裝材料為塑膠,陶瓷。元件的散熱部分可能由金屬組成。元件的引腳分為有鉛和無鉛區別 。