熔噴法工藝原理
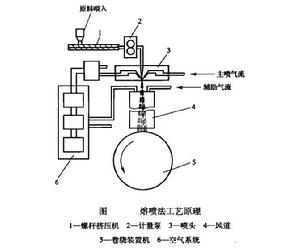
熔噴法的工藝原理如圖1所示。聚合物母粒放入擠出機,並 在擠出機內熔融,溫度在240℃左右(針對聚丙烯一熔噴法採用的主要樹脂)。熔體通過計量泵,到達熔噴模頭。計量泵測量輸出到噴嘴的熔體流量。噴絲嘴是一-排間距不到1mm,直徑在0.2~0.4mm的毛細管。在毛細管的兩側就是進氣孔,加人250~300℃的壓縮空氣。在剛剛形成的聚合物擠出噴絲頭時,壓縮空氣的頭端作用於聚合物,以高於聲速(550m/s)的氣流將熱長絲牽伸至直徑1~10μum,根據其物理特性這種網被稱為微纖網。熱空氣向下流動時與周圍空氣混合,使纖維冷卻並最終固結成短而細的纖維。熔噴法的主要工藝流程如下:
熔體準備→過濾→計量→熔體從噴絲孔擠出→熔體細流牽伸與冷卻→成網
模頭組合件
模頭組合件是熔噴生產線中最關鍵的機械,由聚合物熔體分配系統模頭系統、拉伸熱空氣管路通道以及加熱保溫元件等組成。
熔噴模頭組合件的模頭系統通常由底板、噴絲頭、氣板、加熱元件等組成,是整個組合件中的重要部分。熔噴法非織造布的均勻度與模頭設計、製造有密切關係。通常熔噴模頭的加工精度要求很高,因此熔噴模頭製造成本較昂貴。
結構
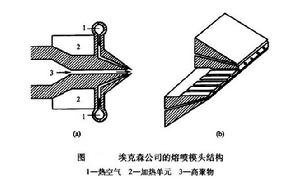
美國埃克森公司生產的熔噴模頭結構如圖2 所示,共有192個噴絲孔,分成4個區域,每個區域有48個噴絲孔,區域之間被25.4mm寬的空間所隔開,該空間用於固定上下兩塊模體,因此該熔噴模頭的噴絲孔實際上是由上下模體配合形成的。先在上下模體結合面上各自加工出微細的凹槽,然後上下模體貼合,校正後可形成一排噴絲孔。
特點
該結構的特點是,可得到較大的噴絲孔長徑比,模頭清潔較方便,但是加工精度和裝配精度要求高。噴絲頭噴絲孔呈單排排列,常用直徑為0.2~0.4mm,長徑比應大於10,孔距為0.6~1.0mm。噴絲孔的加工方法有機械鑽孔、電弧深孔及毛細管焊接加工等。常用的拉伸熱空氣風道夾角為60°,也有設計成90°或30°的。
多排噴絲孔並列排列熔噴機械
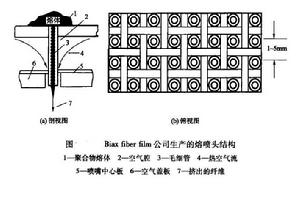
美國Biaxfberflm公司開發出一種具有多排噴絲孔並列排列的熔噴機械,如圖3所示,其熔噴系統結構緊湊,熔噴模頭系統的加熱依靠牽伸熱空氣,沒有其他的電加熱裝置,設備投資較小。此熔噴頭的特點是採用毛細管擠出熔體。聚合物熔體1經過穿過空氣腔2的毛細管3,由空氣板的開孔處擠出。在此區域由熱空氣向聚合物的熱轉移十分有效。毛細管噴絲孔可有1~4排,毛細管間距約1.5mm,因此11.4cm寬的紡絲板可有22~448隻孔。一組紡絲板可有8塊紡絲板,每塊板都有一隻多管輸出的行星泵輸人相同數量的聚合物,而每塊紡絲板的空氣輸人量可單獨調節。幾組紡絲板可並列安裝,形成所需寬度的生產裝置。
聚合物熔體從毛細管中擠出,空氣腔中的牽伸熱空氣從篩網與毛細管組成的縫隙中噴出,並將從毛細管中擠出的聚合物熔體牽伸成超細纖維。由於採用多排噴絲孔,大大提高了生產速度,增加了產量。工作寬度較大時,配置多個計量泵,以保證熔噴纖網單位面積質量的均勻性。該系統通過更換模頭,可生產纖維直徑為1~50μum的熔噴法非織造布。若模頭工作寬度為50.8cm時,產量為300kg/h(纖維直徑為10μm)。