生產
生產波特蘭水泥就是利用礦藏豐富且廉價的原材料進行加工的過程,其原理並不複雜,簡言之,就是將石灰石和黏土或粉土(鐵鋁矽酸鹽)均勻混合,同時摻入少量氧化鐵和石英,將混合物在水泥窯中加熱至1 400~1 600℃,在此溫度範圍內,原料發生化學反應形成矽酸鈣、鋁酸鈣和鐵鋁酸鈣。
首先將原材料磨至細度小於75μm,然後將磨細原材料從旋轉窯頂部的進料口送入窯內。從旋轉窯底部送人燃料(天然氣、油或煤粉),並在窯下部燃燒,熱氣在窯內自下而上流動,這樣在20 min~2.5 h內(具體時間取決於窯的構造)原料自上而下下落的過程中,溫度逐漸升高並發生一系列複雜的化學反應。在窯內溫度最高的部位(熟料帶),液相中開始形成矽酸鈣、鋁酸鈣和鐵酸鈣(已形成並熔融)。當原料下降至窯底部最後一段距離時溫度迅速降低,出窯後即得熟料,熟料呈深色塊狀,直徑為6~50 mm。待熟料冷卻後再與適量石膏混合粉磨至粒徑小於10 μm或更細,摻石膏的目的是為了調節水泥的早期水化速度。
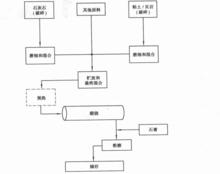
波特蘭水泥的水化
由於水泥顆粒在粒徑和組成上各不相同,所以波特蘭水泥的水化反應相當複雜,得到的水化產物也不盡相同。水化產物的化學組成和微觀結構隨齡期和在混凝土中的位置而變化。
波特蘭水泥水化的基本特徵可簡述如下:
①只要水泥顆粒被水彼此分開,水泥漿就會保持流動性;
②水化產物的總體積大於水泥顆粒的初始總體積;
③當水化產物互相交錯聯生時,拌合物開始凝結;
④隨著水化反應持續進行,水泥顆粒之間形成附加粘結,體系開始形成強度。