粉末冶金製品簡介
粉末冶金製品是採用成形和燒結工藝將金屬粉末(或金屬粉末與非金屬粉末的混合物)製成材料和製品的工藝技術。它是冶金和材料科學的一個分支學科。
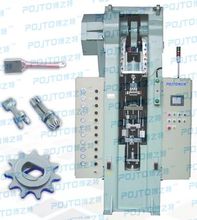
粉末冶金製品的套用範圍十分廣泛,從普通機械製造到精密儀器;從五金工具到大型機械
;從電子工業到電機製造;從民用工業到軍事工業;從一般技術到尖端高技術,均能見到粉末冶金工藝的身影。
粉末冶金髮展歷史:
粉末冶金方法起源於公元前三千多年。製造鐵的第一個方法實質上採用的就是粉末冶金方法。
標誌
而現代粉末冶金技術的發展中共有三個重要標誌:
1、克服了難熔金屬熔鑄過程中產生的困難。1909年製造電燈鎢絲,推動了粉末冶金的發展;1923年粉末冶金硬質合金的出現被譽為機械加工中的革命。
2、 三十年代成功製取多孔含油軸承;繼而粉末冶金鐵基機械零件的發展,充分發揮了粉末冶金少切削甚至無切削的優點。
3、向更高級的新材料、新工藝發展。四十年代,出現金屬陶瓷、彌散強化等材料,六十年代末至七十年代初,粉末高速鋼、粉末高溫合金相繼出現;利用粉末冶金鍛造及熱等靜壓已能製造高強度的零件。
粉末冶金工藝的優點:
1、絕大多數難熔金屬及其化合物、假合金、多孔材料只能用粉末冶金方法來製造。
2、由於粉末冶金方法能壓製成最終尺寸的壓坯,而不需要或很少需要隨後的機械加工,故能大大節約金屬,降低產品成本。用粉末冶金方法製造產品時,金屬的損耗只有1-5%,而用一般熔鑄方法生產時,金屬的損耗可能會達到80%。
3、由於粉末冶金工藝在材料生產過程中並不熔化材料,也就不怕混入由坩堝和脫氧劑等帶來的雜質,而燒結一般在真空和還原氣氛中進行,不怕氧化,也不會給材料任何污染,故有可能製取高純度的材料。
4、粉末冶金法能保證材料成分配比的正確性和均勻性。
5、粉末冶金適宜於生產同一形狀而數量多的產品,特別是齒輪等加工費用高的產品,用粉末冶金法製造能大大降低生產成本。
粉末冶金工藝的的缺點:總體上的缺點:
1)製品內部總有孔隙;
2)普通粉末冶金製品的強度比相應的鍛件或鑄件要低(約低20%~30%);
3)由於成形過程中粉末的流動性遠不如液態金屬,因此對產品結構形狀有一定的限制;
4)壓製成形所需的壓強高,因而製品受壓制設備能力等限制;
5)壓模成本高,一般只適用於成批或大量生產。
金屬粉方面:最終產品的品質難以控制自如;金屬粉昂貴;粉末不順從水力學定律,而使產品結構形狀有一定限制。
製造設備、方法方面:
1)加壓機:常需使用昂貴的強力壓機
2)壓模:屬消耗品,成本較高
3)燒結爐
4)粉末易氧化,混合需長時間
5)製品的尺寸及形狀受限制。
工藝工序
粉末冶金工藝的基本工序是:
1、原料粉末的製備。現有的制粉方法大體可分為兩類:機械法和物理化學法。而機械法可分為:機械粉碎及霧化法;物理化學法又分為:電化腐蝕法、還原法、化合法、還原-化合法、氣相沉積法、液相沉積法以及電解法。其中套用最為廣泛的是還原法、霧化法和電解法。
2、粉末成型為所需形狀的坯塊。成型的目的是製得一定形狀和尺寸的壓坯,並使其具有一定的密度和強度。成型的方法基本上分為加壓成型和無壓成型。加壓成型中套用最多的是模壓成型。
3、坯塊的燒結。燒結是粉末冶金工藝中的關鍵性工序。成型後的壓坯通過燒結使其得到所要求的最終物理機械性能。燒結又分為單元系燒結和多元系燒結。對於單元系和多元系的固相燒結,燒結溫度比所用的金屬及合金的熔點低;對於多元系的液相燒結,燒結溫度一般比其中難熔成分的熔點低,而高於易熔成分的熔點。除普通燒結外,還有松裝燒結、熔浸法、熱壓法等特殊的燒結工藝。
4、產品的後序處理。燒結後的處理,可以根據產品要求的不同,採取多種方式。如精整、浸油、機加工、熱處理及電鍍。此外,近年來一些新工藝如軋制、鍛造也套用於粉末冶金材料燒結後的加工,取得較理想的效果。
發展方向
粉末冶金材料和製品的今後發展方向:
1、有代表性的鐵基合金,將向大體積的精密製品,高質量的結構零部件發展。
2、製造具有均勻顯微組織結構的、加工困難而完全緻密的高性能合金。
3、用增強緻密化過程來製造一般含有混合相組成的特殊合金。
4、製造非均勻材料、非晶態、微晶或者亞穩合金。
5、加工獨特的和非一般形態或成分的複合零部件。